When manufacturing precision optical assemblies at scale, there are two critical areas to consider: efficiency and quality.
It’s a careful balance between these two metrics in the effective manufacture of optical assemblies. Efficiency is often considered the priority in optical systems manufacturing, since it’s critical to keep touch time low and reduce cost of the assembly to create products at a reasonable price point. However, efficiency cannot be prioritized over the quality of the product being manufactured.
The optical assemblies we manufacture at Optikos must be built and verified to their design specifications. They must continue to perform in their fields of use, ranging from aerial mapping and defense applications, to medical devices, to automotive camera systems. In this regard, manufacturing quality is of paramount importance.
At Optikos, we balance the need for efficiency and low-touch time on our assembly lines with functional testing by incorporating custom metrology tools into our manufacturing processes. Often, these tools will be a part of a production step to combine a build process with a functional test.
Being able to balance efficiency and quality in creating high quality systems is the constant struggle of manufacturing divisions across the globe, Optikos included. Here are a few examples of how we incorporate our in-process metrology testing in varying builds in our Building One manufacturing center.
Underwater Camera Assembly (1,000s of units)
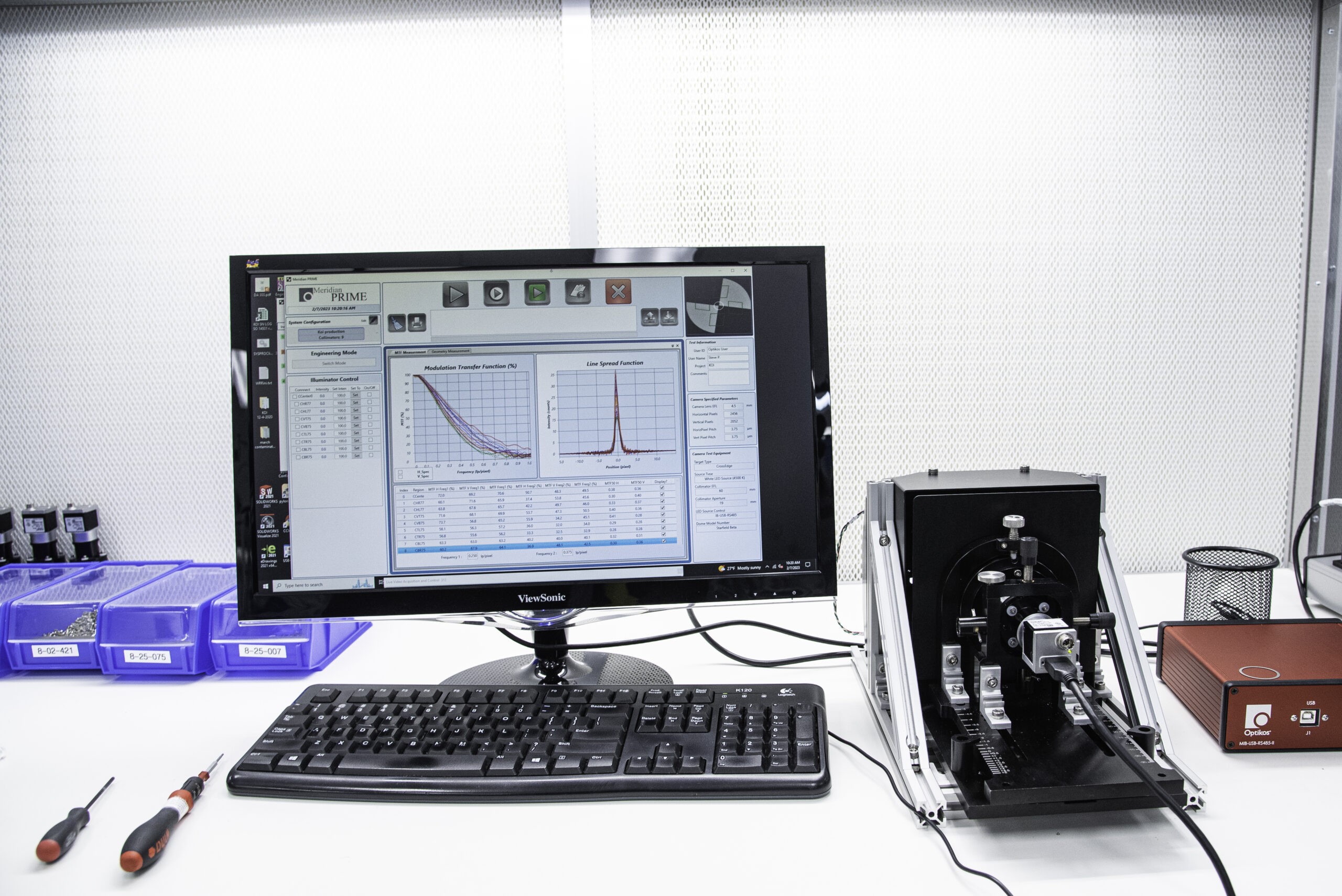
Our first example is a custom Meridian® Starfield™ that is used on an underwater camera assembly. The Starfield™ uses our Meridian® Prime™ software and measures MTF of all field points of the camera under test simultaneously. The camera assembly built on this line includes a lens assembly with a compensation lens group, which allows us to optimize the MTF over the full field of the camera.
Once the lens is compensated and torqued into position on the camera, we have a built-in functional test that adds virtually no time on top of the build process but gives us full field MTF performance of every camera assembly that comes off the line.
VIS-NIR Lens Assemblies (10,000s of units per year)
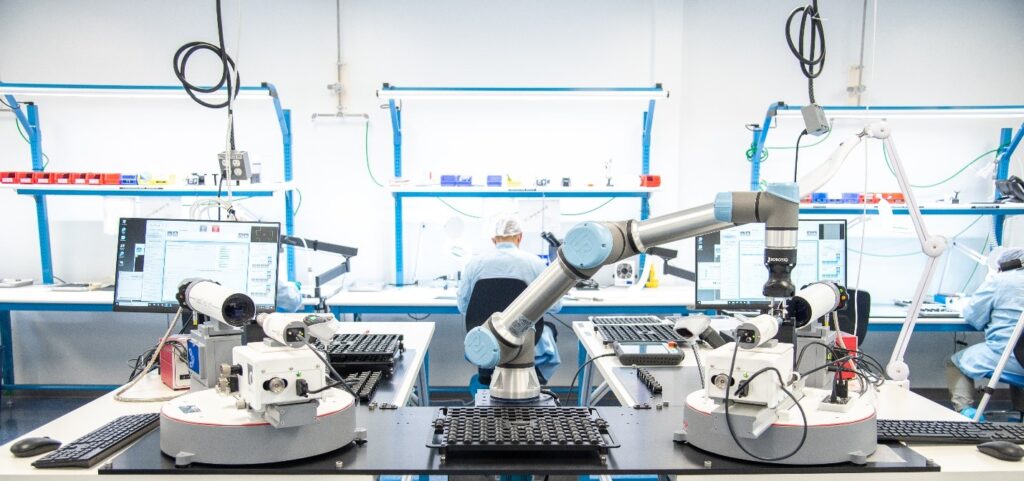
While it is ideal to have functional testing built into the build step, in some cases that is not applicable. When standalone functional testing is required, it is even more critical to develop an efficient process to ensure that the testing does not become the bottleneck of the assembly line.
Optikos undertook a program building 10s-of-thousands of VIS-NIR lens assemblies per year. These lenses were built as drop-in lens assemblies that required 100% functional testing.
To achieve the volumes required, we incorporated a collaborative robot into the assembly line. Trays of the assembled lenses were delivered to the robot, the robot then scanned the exterior barcode on each lens, and loaded one of the two LensCheck™ systems on the assembly line. Each serialized assembly was then measured for effective focal length, on-axis MTF, and off-axis MTF. Passing units were binned, and failing units were separated and quarantined.
By using a collaborative robot interacting with our standard products, we were able to keep up with the high-volume testing demands while adding minimal touch time to the assembly. Each shift of assemblers was able to monitor the robot operation while simultaneously continuing the build process, with the only manual interaction being the replacement of lens trays. An example of this process can be seen here.
Medical Imaging Assemblies (100s of units per year)
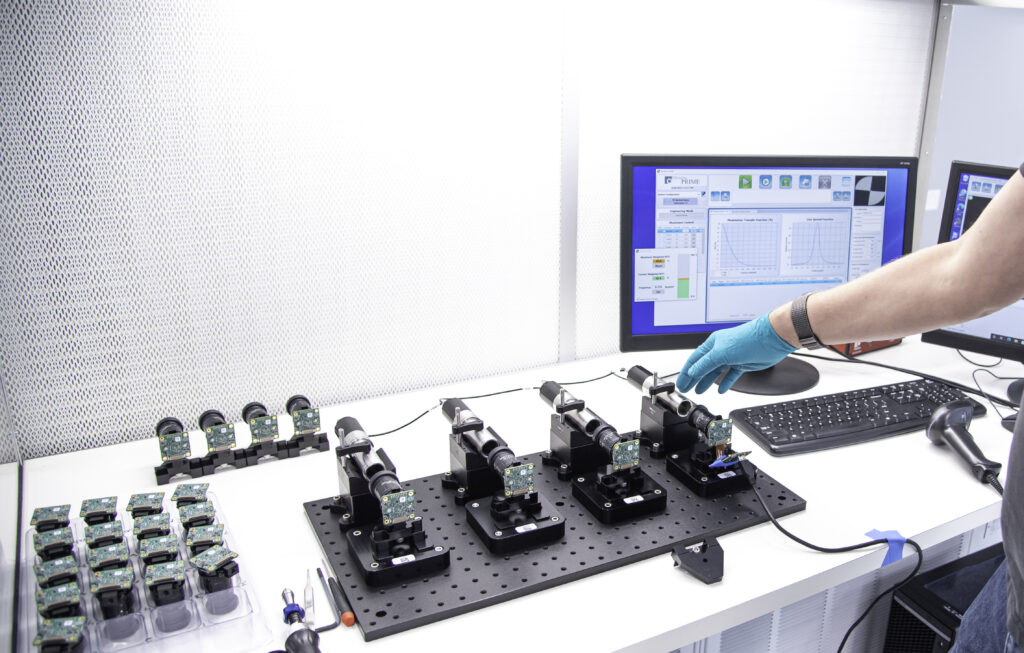
For the medical device community, in-process testing is even more critical to meet stringent product requirements. ISO 13485 requires assembly lines to go through a validation and verification process. By incorporating in-process testing, we can perform this verification testing at the sub assembly level.
We have done this a variety of ways including live optical alignments capturing post-torque images, using custom test fixtures with calibrated equipment to measure radiometric output of illumination devices, and incorporating final functional tests on our OpTest® systems at the end of our assembly lines. Often, we will incorporate functional testing to verify sub assembly level performance. The sub assembly level testing increases our first pass yield at the final functional test and serves to reduce rework time as it narrows the cause of a potential system level failure to a later assembly process.
Regardless of volume and complexity, Optikos can incorporate in-process testing to process steps and/or final functional verification in an efficient manner to ensure your product meets or exceeds expectations.