Anthony Visconti
Optikos Corporation, 107 Audubon Road, Wakefield, MA 01880
Abstract: Precision imaging systems often require diffraction-limited wavefront or other challenging as-built criteria. One method to achieve the desired performance is to include glass melt data in the fabrication process. Compensator selection is presented.
Introduction
Precision optical imaging systems span a wide variety of markets and applications including semiconductor [1], life science, medical device, aerospace, defense, and other industries. Often these imaging systems necessitate demanding performance requirements including diffraction-limited wavefront image quality, pixel or sub-pixel image distortion, and minimized chromatic aberrations. In order for the optical system to be manufactured to these requirements, the design often requires various advanced compensation methods during assembly and test. Such techniques include active alignment of optical elements [2], as-built optimization of compensators during test [3], and airspace compensation based on fabricated measurements including radius, thickness, and glass melt data [4-5].
Melt Data Compensation
Although there are documented methods to reduce the sensitivity of an optical design to glass dispersion tolerance sensitivity [6], some imaging requirements may still require the use of melt compensation. One such technique for melt compensation prescribes element-to-element airspace values for each serial number assembly [7]. This is a multi-step design process. First, measured index of refraction values from glass manufacturers are fit using glass dispersion formulae and interpolated at the design wavelengths of the optical system. Second, the optical design nominal airspace values are re-optimized in the design software to correct for the measured dispersion of the optical glass. Finally, the optimized airspaces are prescribed to the manufacturing and assembly team. There are several techniques for building the imaging system to these prescribed airspaces such as modifying shim thicknesses between elements [8] or more complex methods such as sub-cell alignment turning [9].
Another option one may consider with respect to melt compensation is the use of radii as compensators. With this method, one also obtains index of refraction values from glass manufacturers, utilizes glass dispersion formulae, and interpolates at the design wavelengths. Next, the optical design is re-optimized with radii as variables to correct for the as-measured dispersion of the optical glass. Subsequently, optical prints are revised and optical elements are fabricated. This method has several advantages and potentially several drawbacks. One must recognize the procurement challenges of the raw material for their specific optical design, understand the delivery quantities of the optical system for their customer, and possess confidence in their yield assumptions. Consideration should also be given during re-optimization of the lens design such that changes to the opto-mechanical design are minimized. One may also consider selecting a sub-set of radii as compensators to minimize documentation changes required for procurement. There is an inherent risk in this radius compensation method as mixing glass melts violates the assumptions in the tolerance model and build workflow. However, radius compensation for melt data has performance advantages for some optical systems as evident from the following design example.
Design Example
Three unique Monte Carlo tolerancing routines are performed to simulate different build workflows and demonstrate the effectiveness of melt compensation. The following example is a finite conjugate objective for biomedical imaging as shown in Figure 1. The wavelength spectrum is from 450 to 700 nanometers, and the numerical aperture is 0.2. The object-side full field of view is 4.5 millimeters and the magnification is 3. The object-side working distance is greater than 8 millimeters. The nominal polychromatic root mean square (RMS) wavefront is less than 0.022 waves across the field of view. The as-built performance requirement is for the polychromatic RMS wavefront to remain less than 0.05 waves across the full field of view. Melt compensation is considered in order to meet these requirements.
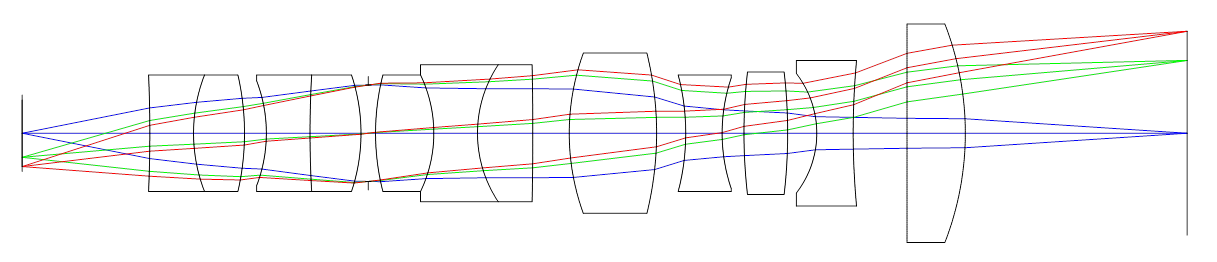
Fig. 1. Nominal optical design raytrace
The first Monte Carlo simulation assumes focus as the only compensator. Glass index (± 0.0005) and Abbe (±0.5%) tolerance ranges are applied to each lens. The second simulation utilizes the airspace between each optical element and focus as compensators. The third routine utilizes the radii of each optical element and focus as compensators. The remaining optical tolerances (radius, thickness, airspace, tilts, decenters, irregularity, etc.) have been omitted. The results of 100 Monte Carlo trials for each scenario are outlined in Table 1. Magnification, focal length, and maximum polychromatic RMS wavefront error are tabulated and the 95th percentile results are shown. Radius compensation has 0.002 waves of image quality degradation with respect to the nominal design, whereas the airspace compensation technique has 0.055 waves of image quality degradation with respect to the nominal design.
Method | Magnification Change (Percent) | Focal Length Change (Percent) | Maximum Polychromatic RMS Wavefront (waves) |
Nominal Design | – | – | 0.022 |
Focus Only | 0.38 | 0.501 | 0.120 |
Airspace Compensation | 0.35 | 0.028 | 0.077 |
Radius Compensation | 0.06 | 0.003 | 0.024 |
It is understood that airspace compensation may still be considered as a viable manufacturing solution for this design if glass index and Abbe tolerances are further tightened for all elements or a subset of the most sensitive elements. It should also be highlighted that some designs are more or less suited for melt compensation, and in some cases, airspace compensation alone may retrieve nominal performance [8]. Alternately, even if a design is suited for melt compensation, it is not uncommon for a specific combination of glass melts to limit the efficacy of melt compensation. In this case, the compensated lens performance may not be regained to a satisfactory level.
Conclusion
Well-characterized tolerance and yield models, controlled build workflows, predictable customer delivery quantities/schedules, and complex procurement processes are often required to execute radius compensation for melt data; nevertheless, radius compensation provides exceptional margin for the remaining tolerances in an optical design in order to meet challenging performance criteria such as polychromatic RMS wavefront.
References
[1] J. Webb, J. Bentley, P. Michaloski, A. Phillips, T. Tienvieri, “Optical design forms for DUV & VUV microlithographic processes,” Proc. SPIE 4346 (2001).
[2] P Langehanenberg, J Heinisch, C Wilde, F Hahne, and B Lüerß “Strategies for active alignment of lenses,” Proc. SPIE 9633 (2015)
[3] H. Chapman and D. Sweeney, “Rigorous method for compensation selection and alignment of microlithographic optical systems,” Proc. SPIE 3331 (1998).
[4] T. Tienvieri and T. Rich, “Optical design compensation from engineering to production manufacturing,” Proc. SPIE 6342 (2006).
[5] T. Tienvieri and T. Rich, “Modern lens design using a lens manufacturing database,” Proc. SPIE 3482 (1998).
[6] S. Sparrold and R.H. Shepard, “An efficient method of reducing glass dispersion tolerance sensitivity,” Proc. SPIE 9293 (2014).
[7] D Stephenson, “Using spreadsheets to recalculate airspaces for diffraction-limited assemblies,” Proc. OSA Vol. 22 (1994).
[8] D Stephenson, “Using Microsoft Excel as a pre-processor for CODE V optimization of air spaces when building camera lenses,” Proc. SPIE 8884 (2013).
[9] J. Kumler and C. Buss “Sub-cell turning to accomplish micron-level alignment of precision assemblies”, Proc. SPIE 10377 (2017).